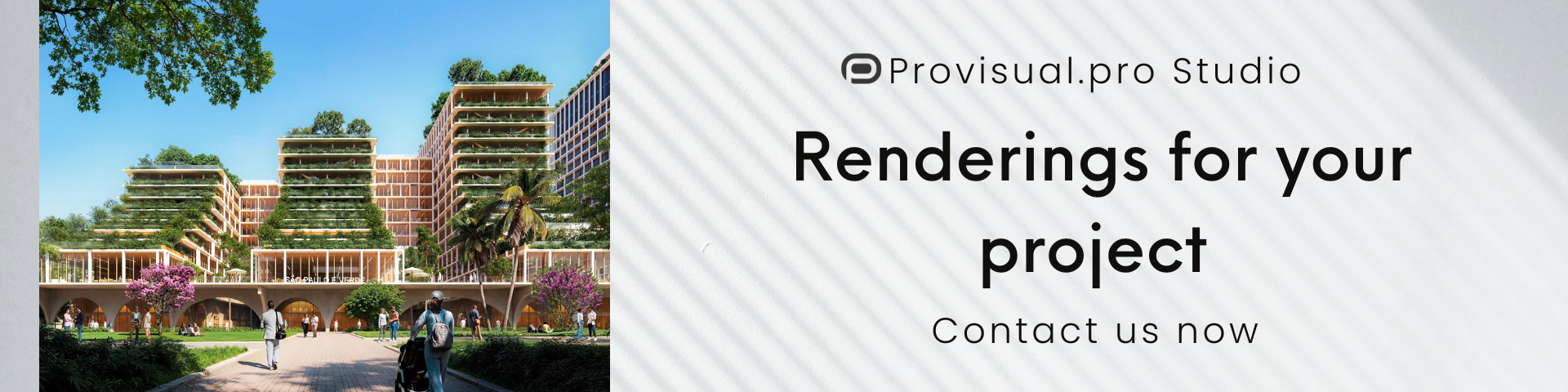
One benefit of 3D printing which we see time and time again, independent of the process of printing being used, is the technology’s ability to help us fabricate new shapes, material properties, and applications for use. When fabricating an object, layer-by-layer, we are able to create objects which would be impossible to do using traditional manufacturing methods. Not only are new shapes possible via 3D printing, but the innovative new printing processes are now able to combine multiple materials in order to distribute different properties over different areas of a particular object. This can be seen with printer’s such as Stratasys’ Objet 500, and continued research efforts are being conducted to further this technology.
In fact, recent research being conducted at the Department of Mechanical Engineering at MIT, headed up by graduate students Mark Guttag and Mary C. Boyce, is taking these processes a step further, into the 4th dimension. We’ve all seen numerous 4D printing applications. Whether it’s materials which fold up when exposed to liquid, or those which change shape based on a variety of outside elements, 4D printing could just be the next evolution in smart materials. For the researchers at MIT, 4D printing has allowed them to change the surface texture of printable structures when certain variables are introduced. They’ve outlined the process in a recent paper called ‘Locally and Dynamically Controllable Surface Topography Through the Use of Particle-Enhanced Soft Composites,’ which has been published in the journal, Advanced Functional Materials.
Basically what the researchers have done, is 3D print objects using multiple materials within a single print. They used a softer, more flexible polymer, sort of like rubber, as well as a harder, much stiffer material, Using a simulation software, they then modeled and simulated an object which consists of both materials. The simulation showed exactly how the object would react to surface pressure. Once satisfied with their creation, they printed it out using a multi-material 3D printer.
“It is demonstrated that a rich variety in periodic and random surface features including variable waves, crease-like features, flat apexes, and valleys can be attained by changing different dimension-less geometric parameters (e.g., relative particle size, shapes, spacing, and distributions),” wrote the researchers. “Furthermore, these surface features can be locally controlled by positioning of particles and do not rely on instabilities.”
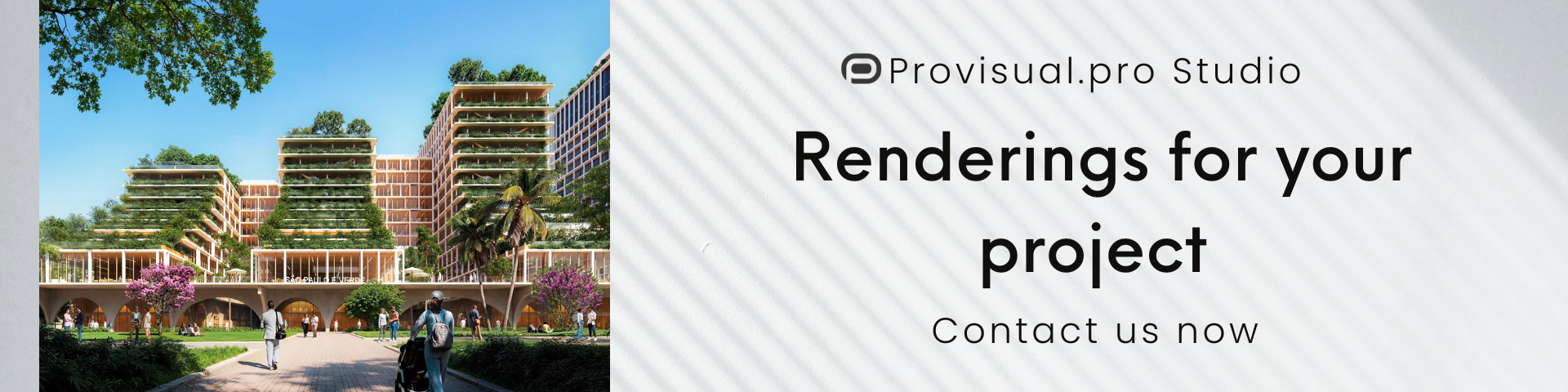
When pressure is placed on the material, a once near-perfectly flat surface undergoes a topographical transformation. Dependent on where the soft and hard materials are located within the object, varying topographical features will appear.
“This is the first-of-its-kind work to create materials with reconfigurable surface texture,” says Yonggang Huang, professor of civil and environmental engineering and mechanical engineering at Northwestern University. “The potential practical impact of this work is huge. It can be used in many applications that benefit from the change of surface, such as in optics and tribology.”
Huang, who was not a part of this research, believes that once this technology is developed, we could see an influx of innovative applications for it, similar to the way in which the 3D printing space has so rapidly developed. Such applications for this technology could include camouflage fabrication, materials which propel, attract, or direct the flow of liquids, reflective materials, and materials which every so often shift, thus limiting the buildup of organisms, such as sea life on the bottom of a ship.
While the research at MIT centered around using pressure as the variable, other variables such as temperature, moisture levels, and electrical charge all could be used to stimulate the material’s transformation. There is still obviously work to be done here, but this is certainly substantial progress within the body of research surrounding 4D printable materials. The research here was funded in cooperation between Masdar Institute of Science and Technology and MIT.
Let’s hear your thoughts on this innovative approach to 4D printing. Discuss in the 4D printed Surface Texture forum thread on 3DPB.com.
If you're looking for affordable 3D visualization services in the USA, our platform provides an ideal solution for all your architectural and real estate needs. Through our service, you can access high-quality 3D renderings at competitive prices without compromising on quality. Whether you need interior visualizations, exterior renderings, or architectural animations, our team ensures that you get professional results that fit within your budget. With our support, you can make your projects visually stunning while saving on costs, all with a quick and straightforward process.
Through our site, you can easily order affordable 3D visualizations for your projects, whether for a residential property, commercial development, or architectural design. We understand the importance of staying within budget, and that's why we offer tailored solutions to ensure you get the best value for your investment. Our experts work efficiently to provide you with realistic, photorealistic 3D images that will elevate your presentations and attract clients, making your property stand out in the market.